Reducing CO2 Emissions in Daily Operations
JAL Green Operations
The JAL Group is conducting various activities to reduce CO2 emissions on the premise of safe flight operations. These activities are collectively called "JAL Green Operations".
The Group is implementing CO2 emission reduction initiatives through the cross-organizational Fuel-Saving Project in order to achieve net zero CO2 emissions.
In FY2023, we steadily implemented various initiatives, including efforts to devise flight plans, which resulted in a 2.4% reduction compared to the FY2025 target of 2.5% of total emissions.

Preparing for Departure
1.Optimized flight plans
When flying, we obtain the latest weather information on the route and destination for each flight, and make a flight plan based on the information such as the number of passengers, cargo weight, taking safety, comfort, and punctuality into consideration, and try to minimize fuel consumption.
In particular, the precise prediction of cargo weight has a significant impact on the optimization of fuel loading when making flight plans, so we are working cross-organizationally to implement the precise prediction at an appropriate time before departure and reflecting it in flight plans.
In addition, the UPR (User Preferred Route) system has been adopted for Pacific routes (Hawaii, Australia, and the west coast of North America). Rather than the conventional method of selecting a flight route from among several routes designated in advance by air traffic control, UPR allows airlines to set their own routes based on weather conditions and other factors. This allows airlines to fly the most desirable routes, leading to reduced fuel consumption and thus reduced CO2 emissions.
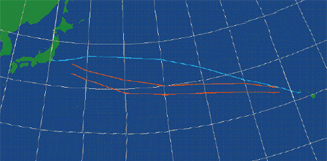
Example of UPR
Blue line: Example of UPR from Narita to Honolulu
Red line: Conventional flight paths
2.Reduction of aircraft weight *() shows weight reduction per flight
Reducing the weight of aircrafts decreases fuel consumption and CO2 emissions. JAL is proactively working to reduce the weight of various onboard equipment.
Proactive use of lightweight containers (Tokyo-London: 391kg)
Since 2014, JAL has been progressively introducing lightweight containers.
The lightest types weigh about 60kg, compared to the conventional containers which weigh about 100kg.
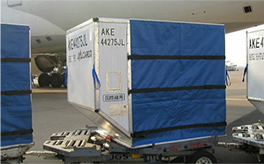
Lightweight container
Optimization of the amount of water loaded for in-flight use (Tokyo-London: 390kg)
The amount of water carried on board is fine-tuned to suit the route and type of flight, based on actual usage.
Revision of standards for the carriage of drinks and snacks in-flight (Tokyo-London: 113kg)
On international flights, the loading standards for beverages and snacks specified for each route and class of service have been reviewed. The daily booking volume is being checked in order to determine the right amount to be loaded on each flight.
Weight reduction of in-flight magazines (Tokyo-London: 151kg)
In order to reduce paper usage and the weight on board, page numbers of the international in-flight entertainment magazine "JAL Mooove!" were reduced and integrated into "SKYWARD" in May 2021.
Reduction in amount of dry ice used to refrigerate beverages (Tokyo-London: 26kg)
As the use of dry ice leads to increasing CO2 emissions, the weight of loaded items are optimized by verifying the remaining amount and the temperature of beverages upon arrival of each flight.
On domestic flights, ice packs instead of dry ice have been used since 2003, which resulted in significant reduction of CO2 emissions.
Weight reduction of cabin carts (Tokyo-London: 212kg)
Since 2019, weight of cabin carts used on board for serving meals is being reduced.
Each of these cabin carts are 7.6 kg less compared to the previous model.
*Conducted on domestic flights operated by Airbus A350 and Boeing 787 aircrafts.
While Parked in spot
3.Reduce APU usage
Aircraft need power and air conditioning for cabin lighting even while parked on the ground.
Therefore, an auxiliary power unit (APU) is installed in the tail of many large passenger aircraft. The APU has the same structure as a small jet engine, It runs on fuel, and therefore emits a certain amount of CO2. APU is essential for starting the engines for pushback, during which an aircraft is pushed backward away from the spot by a towing truck to the taxiway that leads to the runway.
At departure, a delayed APU start to shorten APU usage can contribute to reducing CO2 emissions. When the APU is not used, power and air conditioning are supplied by a ground power source, which is more efficient than the APU and effective in reducing CO2 and noise emissions, as the APU is designed for installation on aircraft.
The JAL Group strives to shorten APU usage and reduce CO2 emissions during pre-flight preparations without compromising passenger comfort through the coordinated teamwork of its flight crew members, maintenance engineers, and ground staff. For example, more than 100 kg of CO2 emissions can be reduced at Haneda Airport by switching power and air conditioning supply from the APU of a Boeing 777 to a ground power source for 10 minutes.
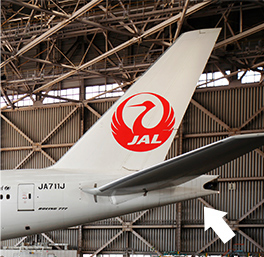
The auxiliary power unit (APU) is installed in the tail.
4.Closing window shades
When aircrafts are parked in the spot, window shades (sunshades) are lowered depending on the weather and the time of day, with cooperation from passengers. Air-condition is supplied from the APU installed in the tail or a ground power source to maintain comfortable cabin temperatures. However, as the APU runs on fuel, it emits CO2. Therefore, by lowering window shades and maintaining appropriate cabin temperatures, air-conditioning use can be shortened, thus reducing unnecessary CO2.
*This activity has been suspended in response to covid-19
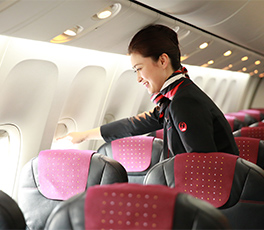
Window shades are lowered depending on the weather, etc.
At Take off
5.Ascent with early acceleration
Ascending after takeoff while accelerating from an earlier point is effective for reaching cruising altitude earlier in the flight and reducing fuel consumption. Therefore, JAL is actively utilizing this approach to reduce CO2 emissions.
In Flight
6.Adjusting flight speed
Airlines plan and operate their flights to ensure that they arrive at the destination airport on the time stated in the timetable. However, since the congestion at the departure and destination airports and the weather conditions (especially wind speed) in the air differ day by day, the flight speed is adjusted accordingly.
In the case of a flight with a weak headwind or a strong tailwind, and the arrival time is much earlier than planned, we adjust the flight speed to more fuel-efficient, thereby reducing CO2 emissions.
During the Descent Phase
7.Continuous Descent Operations
Aircraft climb and descend stepwise with level-off portions in-between according to instructions of ATC, resembling a staircase (figure below).
In the descent phase to prepare for landing, the aircraft descends to a lower altitude by operating at lower engine thrust or idle thrust.(Keep the engine running to a minimum )
Then the pilot waits for instructions from ATC to descend to the next altitude. During level flight, the pilot must increase power to keep the aircraft level. Long segments of level flight increase fuel consumption and CO2 emissions.
To eliminate such inefficiencies, the descent path is identified in advance through ATC-pilot communications and the pilot performs the continuous descent approach along the glide slope to the runway.
At Helsinki International Airport, Kansai International Airport, and Kagoshima Airport, where continuous descents are in operation during specific hours, the JAL Group actively uses this process. As a result, CDOs(Continuous Descent Operations)reduced not only CO2 emission, but also pilots' workload by reducing the frequency of communication with ATC, and contributed significantly to flight safety.
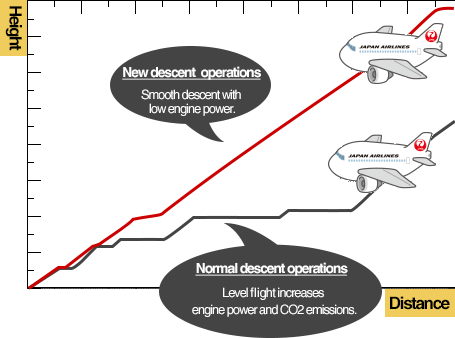
8.Reduced Flap
The wings of an aircraft change shape at the landing phase so that the approach to the ground can be flown more slowly to maintain safety. At this time, flaps are extended from the rear edges of the main wings.
This enables the wings to produce more lift at slower speed, but increases air resistance (drag) at the same time. Flap angles differ depending on aircraft type. A longer flap will produce more lift but also more drag because of the increased projected area. When large angle flaps are used, higher engine thrust must be maintained, which increases fuel consumption and CO2 emissions.
Therefore, when conditions such as when landing on a long runway, allow the pilot will select a smaller flap angle (reduced flap) to perform the final approach until touchdown, which will contribute to reducing CO2 and noise emissions on the ground.
9.Delayed Flap & Gear
Landing gears (arrows) and flaps (circles), which are essential mechanisms for landing, produce large amounts of drag, and to overcome the drag on the aircraft, the engines need to produce extra power. Flaps and landing gear are indispensable at landing, but for aircraft, extension of landing gears and flaps produce more drag than in cruise, resulting in greater fuel consumption and CO2 emissions.
To reduce CO2 emissions, the pilot delays flap and gear extension depending on conditions at landing.
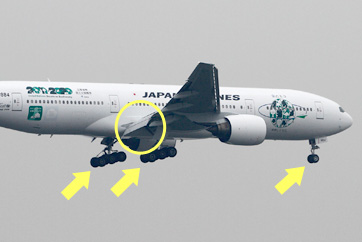
Photo: Hisao Furugaya
At Landing
10.Idle Reverse
After landing, the aircraft decelerates appropriately on the runway, exits the runway, and proceeds to the specified taxiway. Reverse engine thrust and the brakes in the landing gears are used to slow down, but the thrust reversers have the greatest effect when decelerating at high speeds immediately after touchdown. The engine's mechanical structure diverts thrust so that it acts against the forward travel of the aircraft and provides deceleration. This is powered by rotations of the engine.
The greater the reverse thrust that is applied, the faster the engine rotates. If conditions allow at landings, such as a strong headwind or a dry runway, the aircraft can decelerate by using reverse thrust at idle (Keep the engine running to a minimum) power. Therefore, to reduce CO2 emissions, the pilot determines landing conditions and applies reverse thrust if sufficient deceleration can be achieved.
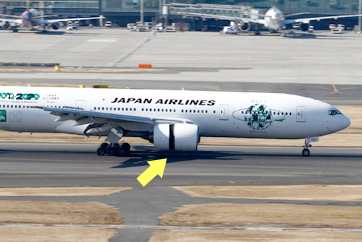
Photo: Hisao Furugaya
Reverse thrust after landing (engine cowls open up)
11.Single-Engine-Taxi-In
When taxing to the parking spot afer landing, only one engine is used, if certain conditions are met, to reduce CO2 emissions.
Efforts outside of operations
12.Engine washing
Aircraft engines get dirty as they ingest and accumulate airborne particles in flight, which in turn reduces fuel efficiency and increases CO2 emissions. The JAL Group regularly washes the engine interior to remove particles that have adhered to internal components during flight. This contributes to approximately 1% recovery of fuel efficiency. Engine washing is performed every 200 to 300 days.
In February 2022, the JAL Group became the first company in the world to introduce foam cleaning to regional jet engines.
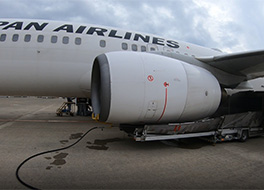
Engine washing
13. Improvement of Wing Tips and Fuselage, as well as Riblets
The tips of wings were straight on conventional aircraft however, by curving them, wing tip vortices that occur at the wing tips can be reduced as well as drag, thus improving fuel efficiency and reducing CO2 emissions.
As the benefits of winglet on fuel economy was expected, the JAL Group revamped nine Boeing 767 aircraft operated on long-haul routes. On recent models of aircraft, the Boeing 737-800 and 787and the Airbus A350 have winglets or wing shapes that have similar effects.
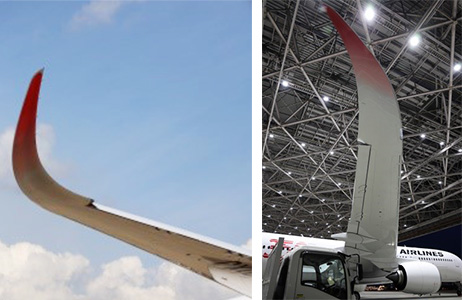
Winglets
In addition, JAL, together with research institutes and technology manufacturers, is conducting the world's first flight demonstration test of an aircraft with a riblet applied on the paint film of the fuselage exterior. When this technology is put into practical use, it is expected to improve fuel efficiency by up to 2% and make a significant contribution to CO2 emission reduction. In the future, we plan to expand the use of this technology to international flights.
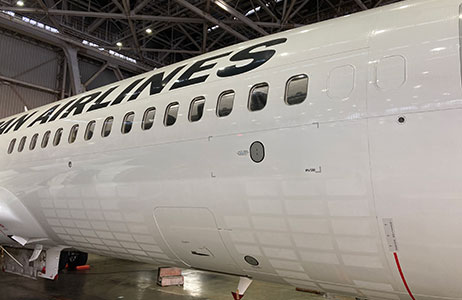
14.Engine Upgrades and Replacement
JAL Group Boeing 787 aircraft are fitted with General Electric GEnx-1B engines. Various design changes called PIP (Performance Improvement Program) have been undertaken to improve engine performance. There are currently two types, PIP-1 and PIP-2.
The PIP-2 engine is an improved version of the PIP-1 engine with significantly improved designed parts. By improving the low-pressure compressor, high pressure compressor, combustor and high-pressure turbine, fuel efficiency has improved approximately 1.2% compared to the PIP-1 engine.
The JAL Group plans to upgrade all PIP-1 engines to PIP-2 engines, in consideration of environmental impacts of engines.
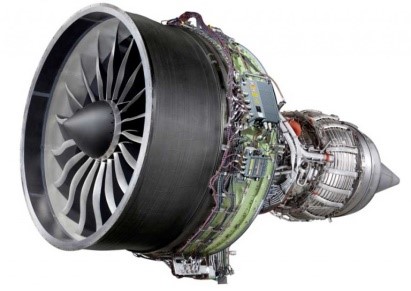
GEnx-1B engine installed on the Boeing 787