Implementation of Safety Management System
We implement the safety management system (SMS) in accordance with the safety management policy to ensure that the SMS functions smoothly.
Safety Information Gathering and Dissemination
Information Gathering
In collecting information related to safety, we collect and analyze not only manifest but also latent information, identify hazards, and take preventive measures to prevent recurrence of aviation accidents and other incidents that may affect safe operations, as well as preventive measures.
Safety-related information is collected from a wide range of sources, including reports from various departments regarding unsafe incidents, flight data analysis programs, as well as crew fatigue risk management programs and alcohol-related risk management programs, and used to prevent the occurrence of unsafe incidents. Since FY2021, we established a management policy on crew fatigue risk and made efforts to gather further information.
Fatigue Risk Management Program
In order to contribute to the improvement of flight safety and quality, we gather data to manage fatigue-related risks among pilots and cabin crew and take appropriate corrective action based on the gathered data.
(Fatigue Risk Management Policy)
It is recognized that fatigue risk of flight crew and cabin crew is an inevitable hazard that exists during an operation, and the company shall endeavor to effectively manage and reduce fatigue risk of flight crew and cabin crew to improve flight safety. JAL's fatigue risk management applies to all operations conducted by the company and is implemented through continuous, data-driven risk management based on scientific insight and performance. Fatigue risk management consists of stakeholders exercising the following responsibilities (Shared Responsibility).
Dissemination to the Employees
The collected information is disseminated to JAL Group employees in internal documents to prevent the recurrence of unsafe events and to raise safety awareness.
The main media for sharing safety information are as follows:
- Corporate Safety, an internal document providing the JAL Group's internal safety policy
- “Safety” webpage of JAL’s website
- ”Safety” webpage of our intranet
- Safety magazine ”FLIGHT SAFETY”
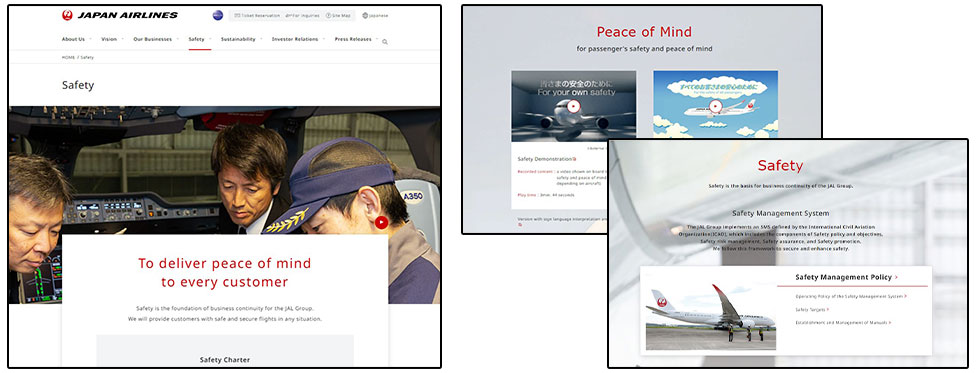
“Safety” webpage of JAL’s website
Safety Risk Management
The JAL Group manages safety risks through the following step-by-step process, establishes measures to ensure safety, and deals with accidents and events appropriately.
Identify hazard
Utilizing gathered information on unsafe conditions and unsafe events, we identify hazards and real or hidden risk factors with the potential to cause or contribute to an aircraft accident or serious incident. All safety events within the JAL Group are managed and shared in a common JAL Group database (JSD).
We have established an environment that facilitates and encourages reports from staff on unsafe behavior they have experienced or unsafe conditions they have found, and the resulting events (safety events).
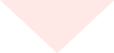
Assess risk for Identification of the main risks
We determine the severity of consequences and the probability of occurrence, assess the acceptability of the risk level and examine the need to take action. In addition to risk assessment by departments where risks have emerged, the Corporate Safety and Security Division assesses hazards within the Group using Event Risk Classification (ERC) to detect potential risks as early as possible.
■ Risk assessment by Event Risk Classification (ERC)
Events are assessed from the viewpoint of the likelihood of hazardous events and the effectiveness of current control mechanisms (safety barriers) in order to strengthen proactive prevention of accidents. We also monitor the trend of concentration and frequency of events by scoring the risks and plotting them in each field for a certain period of time. When the cumulative score exceeds the threshold, we identify the safety issue and take mitigation measures, as necessary.
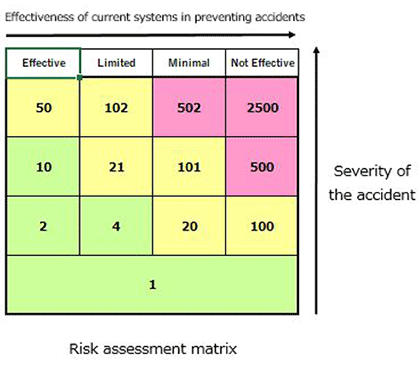
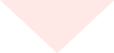
Establish measures
Each department establishes and implements measures to eliminate each hazard so that high priority risks are reduced to a tolerable level.
■ Causal analysis by Human Factors Analysis and Classification System (HFACS)
In order to reduce human error, we analyze not only unsafe behavior but also a wide range of factors such as procedures, working environments and organizational impacts, and take measures against underlying risk factors. We also statistically analyze the identified factors and address potential organizational issues to proactively prevent.
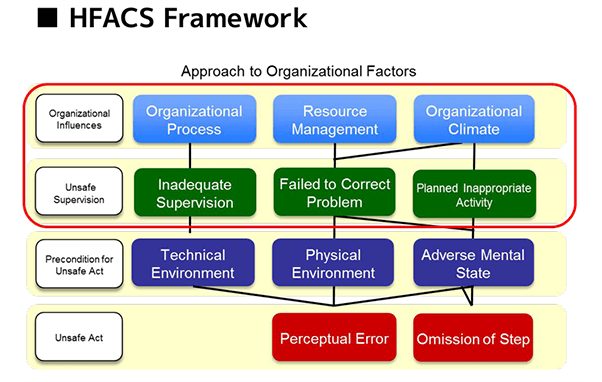
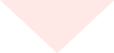
Monitor and review
Monitor the implementation of measures and evaluate their effectiveness. If the risk level is determined not to be acceptable, additional measures are established and implemented to ensure that the safety management system functions effectively.
Examples of risks identified by ERC and mitigation measures
-
Case 1
Falling Baggage -
Case 2
Animals on Runway -
Case 3
Falling Baggage -
Case 4
Caught in Seat -
Case 5
Trash Can Burst out
【Unsafe Event】
Multiple occurences of falling baggage from the center overhead stowage bins of the B767 during takeoff or landing.
Identify hazard
Investigation revealed that the latch mechanism easily unlocked.
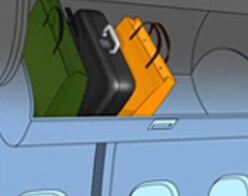
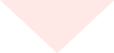
Assess risk
ERC assessment of onboard injuries revealed that the 90 day-cumulative value exceeded the threshold. It was designated a Safety Issue.
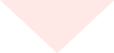
Establish measures
・Non-slip tape was installed in the overhead bins.
・Latches were replaced with the improved model.
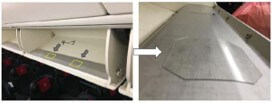
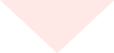
Monitor and review
No new events reported since then.
【Unsafe Event】
Large wild animals (deer) entered the runway of New Chitose Airport in winter.
Identify hazard
Investigation revealed that the fence was low enough for deer to step over due to accumulated snow in the area where the animals entered.
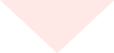
Assess risk
ERC assessment of aircraft damage and runway excursion rated this event as yellow.
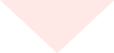
Establish measures
Snow was removed regularly by the airport authority.
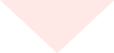
Monitor and review
No new events reported since then.
【Unsafe Event】
Multiple occurences of falling baggage from the overhead stowage bins of the A350 during takeoff or landing.
Identify hazard
Investigation revealed that a half-latch condition may occur if the overhead stowage bin door is not properly closed.
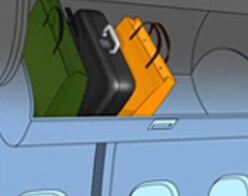
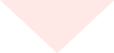
Assess risk
ERC assessment of onboard injuries revealed that the 90-day cumulative value exceeded the threshold. It was designated a Safety Issue.
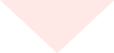
Establish measures
Procedures for cabin attendants to visually and tactually check that the overhead stowage bin door is properly locked were revised.
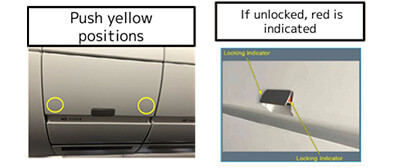
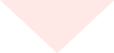
Monitor and review
No new events reported since then.
【Unsafe Event】
A child aboard a B777 got caught in a Business Class electrical seat when the child touched the seat recline button.
Identify hazard
Investigation revealed that even though the seat is designed to prevent movement of the seat when an object is caught in the seat, the mechanism does not work if the object is small.
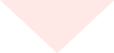
Assess risk
As a result of ERC assessment of onboard injuries, it was designated a Safety Issue.
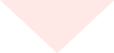
Establish measures
Precautionary information is provided to passengers with a leaflet and by cabin attendants.
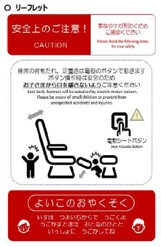
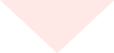
Monitor and review
No new events reported since then.
【Unsafe Event】
On the A350, the storage door in the kitchen opened and the trash can inside fell forward.
Identify hazard
It was found that when the aircraft tilted forward during landing, the storage door would open if the latch was not locked.
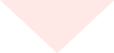
Assess risk
There was possible that injury could occur to passengers and the crew.
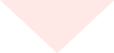
Establish measures
Attention was called to the crew about the way to push the latch and how the angle should look.
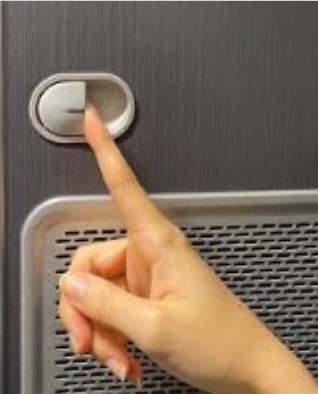
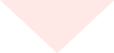
Monitor and review
No such cases occurred after the measures were implemented.
Emergency Response
Procedures for aircraft accidents, serious incidents and affairs are documented in the Aircraft Accident Handling Manual. In the event of an accident or a serious incident, an aircraft accident investigation committee or a serious incident review meeting is organized and causal investigation and review of countermeasures are conducted.
Procedures for other than aircraft accident, serious incidents and affairs are documented in the Risk Management Manual.
Disaster Measures
As natural disasters have become more frequent and severe, affecting social and economic activities including everyday life, it has become imperative for transport business operators to improve their preparedness for disasters to reduce and prevent the spread of damage, maintain business activities, and resume operations as quickly as possible. Under these circumstances, the JAL Group has established the JAL Group Disaster Handling Regulations and has built a framework to prevent and reduce damage by strengthening preparedness.
Internal Audits
The JAL Group conducted internal audits in accordance with safety management regulations to confirm that the SMS complies with laws and internal regulations and that the system is properly operated and functioning effectively. In addition, the IATA Operational Safety Audit (IOSA) registered companies, JAL, J-AIR, and JTA, have conducted internal audits based on IATA requirements to ensure compliance with the standards set by IATA (IOSA standards).
Management Review
The JAL Group conducts management reviews of policies, plans, and various information at the Group Safety Committee chaired by the President, with the aim of ensuring that top management regularly and continuously evaluates the effective functioning of the SMS and directs improvement as necessary.
Management of Change
Expansion and downsizing of organizations or changes to facilities, systems, processes and procedures due to internal and external changes in the environment may unintentionally create new hazards or affect existing risk mitigation measures. The JAL Group has established a process of Management of Change to ensure that safety risks associated with change are addressed.
Third-party Assessment
Ministry of Land, Infrastructure and Transport(MLIT)
The JAL Group undertakes audits and assessments conducted by the MLIT. We take necessary countermeasures for their findings or recommendations.
IATA Operational Safety Audit (IOSA)
IOSA is an international safety audit program designed to ensure that an airline’s SMS is functioning effectively. In the JAL Group, JAL, JTA, and J-AIR are IOSA-registered airlines. IATA member airlines are required to undergo an audit regularly.
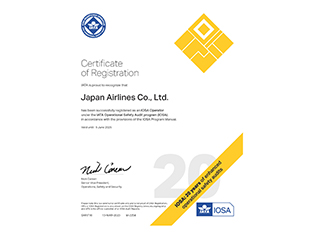
Safety Advisory Group
In August 2005, JAL requested five experts with extensive knowledge and experience in human factors, analysis of failures and defects, organizational management and culture, and safety to provide the company with objective advice and recommendations. This external panel of experts, called the Safety Advisory Group, provides a wide range of safety advice and recommendations from a professional perspective, which are used in management and safety operations of the JAL Group.
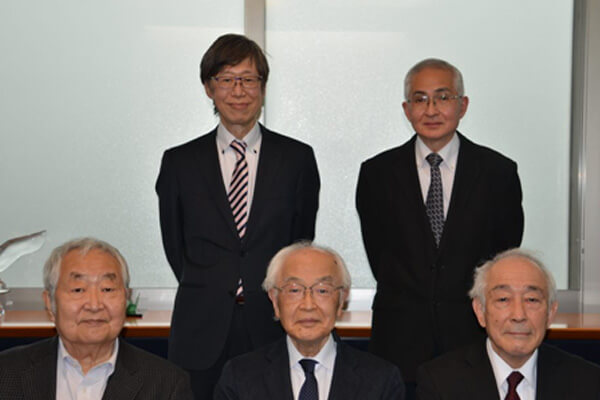
Members of Safety Advisory Group
Back row, from left, Prof. Haga, Prof. Komatsubara
Front row, from left, Prof. Hatamura, Mr. Yanagida (Chair), Prof. Kamata
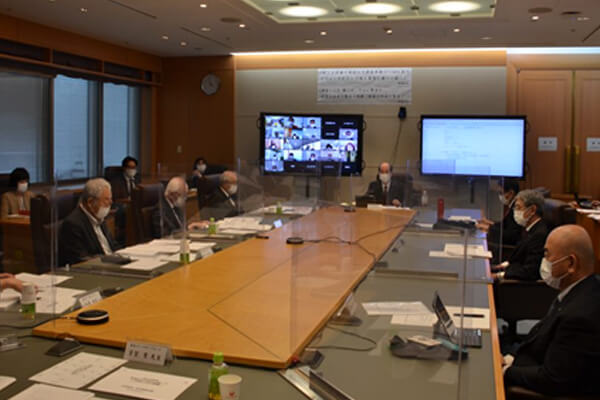
Follow-up meeting with management
Education, Training and Safety Awareness
The JAL Group provides education and training according to the role and position of each employee to equip them with the skills, knowledge and abilities necessary for safety-related duties. We also share necessary safety information and conduct Safety Education regularly.
Initiatives based on the Three Actuals Principle
The Three Actuals Principle is a concept advocated by Prof. HATAMURA Yotaro of the Safety Advisory Group that frontline staff can understand the essence of accidents by going to the “actual place,” seeing the “actual object” (parts of remaining aircraft, personal belongings of the victims, etc.) and listening to stories of the “actual people” who experienced the situation at the time of the accident.
JAL Group staff climb the Osutaka Ridge, "the actual place" of the accident, to console the souls of the victims, and see remaining parts of the aircraft and other "actual objects" in the Safety Promotion Center. By watching news videos of the accident and listening to talks from the “actual people,” the JAL Group employees reaffirm the importance of safety from the depths of their mind.
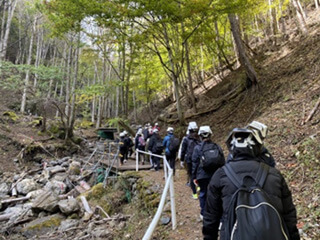
for New Employees
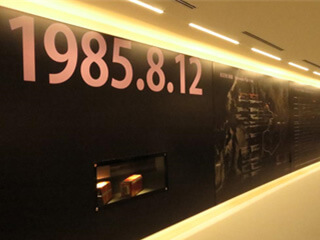
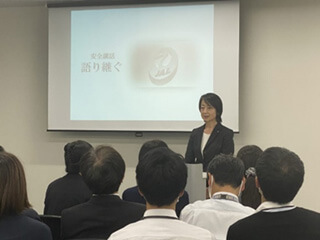
Listening to talks from the “actual people” who experienced the accident
Safety Education
In order to maintain safety, which is the basic foundation for business continuity of the JAL Group, we provide employees with knowledge, skills and abilities necessary for their everyday duties and education to develop employees with a high level of safety awareness.
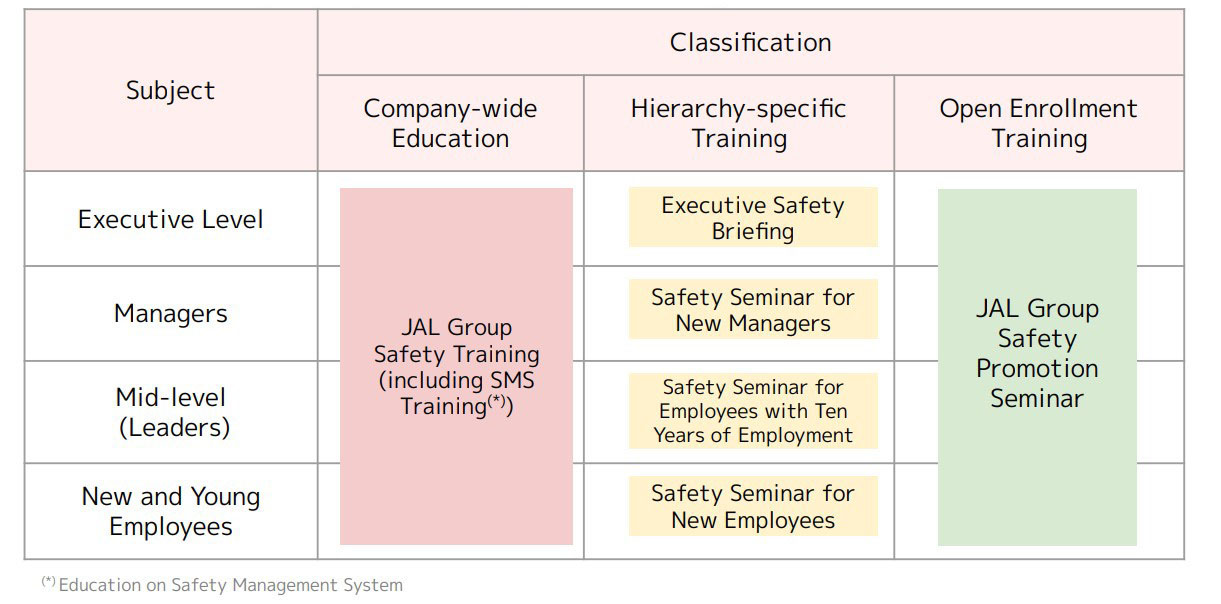
Safety education common to the JAL Group
All JAL Group employees receive Safety Education regularly to re-evaluate safety associated with their duties and to foster an awareness that safety is the basis for business continuity of the JAL Group. In addition, the JAL Group and other companies and industries conduct annual education to raise awareness again by reflecting on drinking problems and to reconfirm correct knowledge about alcohol to ensure thorough self-management.
Safety Training by JAL Group Hierarchy
Based on the Three Actuals Principle (“actual place,” seeing the “actual object” parts of remaining aircraft, personal belongings of the victims, among others), we will think about safety through a memorial climb to Mt. Osutaka, a tour of the Safety Awareness Center, and watching videos of people who were directly involved in the accident. Finally, a Safety Pledge was created to put their thoughts into action and linking them to our daily actions.
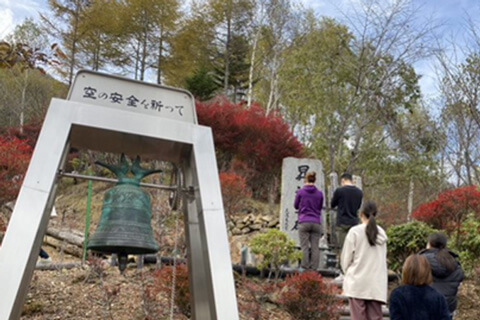
A memorial climb up the Osutaka Ridge
Safety Promotion Seminar
For JAL Group employees and subcontract staff, we hold seminars where employees voluntarily participate, such as a tour of the Safety Promotion Center, a memorial climb to Mt. Osutaka, a second to the third person perspective(*) seminar, and a safety seminar for interindustry exchanges. We strive to raise safety awareness through the participation of employees from both domestic and overseas job categories and regions by holding conversations about safety.
*The second to third person perspective: In order for each and every employee of the JAL Group to think from the customer's perspective, we value the second to third person perspective, which combines the third person perspective of an aviation professional with the first person perspective (if I were onboard) and second person perspective (if my family were onboard) . We are committed to the second to third person perspective, which combines the first and second person perspectives.
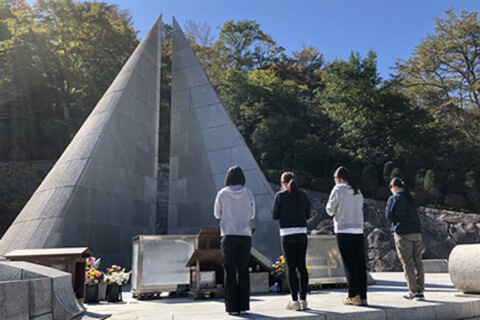
Praying at Irei-no-Sono Monument
A Safety Culture
Safety culture is part of the organizational culture, the common safety awareness among everyone in the organization and maximizes the function of the safety management system (SMS).
The JAL Group is committed to fostering safety awareness and safety culture based on the second to third person perspective and Three Actuals Principle as lessons learned throughout our history. Furthermore, to build on the safety awareness and safety culture we have cultivated and further strengthen the SMS functions, we have established four elements namely a just culture, a reporting culture, a flexible culture and a learning culture. In addition, we will further foster a safety culture by having all JAL Group employees act on our shared values, thereby strengthening the SMS.
A Just Culture
A just culture is also known as a culture of trust. The JAL Group's Safety Management Manual stipulates that “all employees’ safety decisions and acts are respected and tolerated, regardless of the outcome.” This is based on the premise that employees act as safety professionals and contribute to the safety of operations with their knowledge, skills, and abilities. However, when a truly unacceptable behavior occurs, it will be dealt with strictly, and even in the case of an acceptable behavior, measures will be taken to restore, maintain, or improve safety. By ensuring transparency and consistency, employees can act with safety and peace of mind without fear of any disadvantages. The JAL Group considers this just culture to be a prerequisite for the other elements and promotes employee understanding.
A Reporting Culture
For proper safety management, it is essential to report unsafety hazards and all potential unsafe elements. We have implemented a voluntary reporting system, enabling employees to report even minor human errors. These reports are subsequently utilized in our preventative measures. As transparent and consistent responses are carried out based on this just culture, establishing an environment for reporting with confidence and encouraging employees to feel comfortable voicing their concerns.
A Flexible Culture
In order to ensure safety even in unforeseen circumstances, it is necessary to understand the purpose and background of established rules and regulations, and to accumulate knowledge of various response cases. We are working to ensure that all employees can always inquire why these procedures are implemented and to understand the real reason for the guidelines. We are also working to improve our decision-making process so that we can respond flexibly to changes in circumstances, such as reviewing staff assignments, increasing staff as necessary, and delegating authority.
A Learning Culture
The JAL Group aims to achieve sustainable growth and development by adapting to rapid environmental changes. In order to continuously improve safety, we are constantly implementing the best safety measures through an ongoing cycle of improvement. This includes regular reviews and updates of manuals, as well as the optimization of our organization, facilities, and business plans.
Safety-related communication
In addition to top-down communication from top management to frontline divisions, the JAL Group is committed to interactive communication from the bottom up, from frontline divisions to management. In addition, we are working to foster a culture of safety by focusing on workplace culture and employee satisfaction through a variety of initiatives, such as creating an atmosphere in the workplace where employees can easily express their opinions and seek advice, and paying tribute to the contributions of employees who work diligently in their daily duties.
Communication Leader Meeting (CLM)
The CLM is a meeting where employees in various occupations and divisions assemble from all over Japan to communicate with each other to create an open corporate culture, promote autonomous activities, and strengthen frontline capabilities. This is an initiative to bring co-workers together to make connections and broaden their perspectives by discussing and solving active or latent issues within the JAL Group.
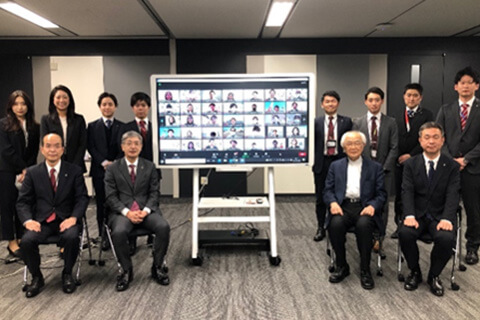
CLM Activities Reporting Meeting for Management
Workplace visit by executive officers
The JAL Group provides opportunities for top management and executive officers of Flight Operations, Engineering and Maintenance, Cabin Attendants, Airport Operations, Operations, Cargo and Mail, and other production divisions to visit frontlines on a regular basis to communicate directly with our employees. During the Semiannual Safety Campaign and the Year-end and New Year Safety Inspection, executive officers of general managing divisions such as General Affairs, Accounting, Human Resources, and IT Planning, as well as production divisions, visit airports in Japan and overseas to try to identify the issues at the frontlines.
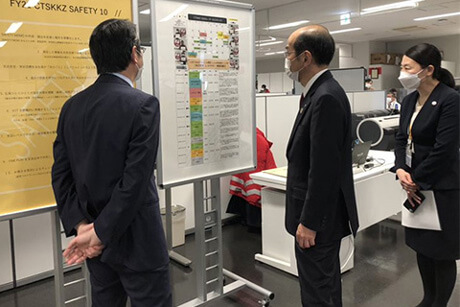
Workplace tours by executive officers
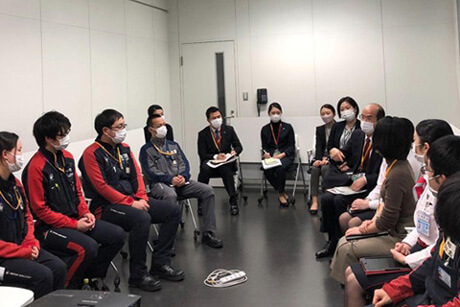
Round table meeting between employees and management
Employee recognition awards
The JAL Group awards the employees with the aim to foster a culture to compliment each other and enhance safety awareness. Employees are awarded for such actions as proactively preventing events that affect safe operations by acting in accordance with the Safety Charter or analyzing and reporting irregularities, and contributing significantly to sharing knowledge and actively preventing recurrence. Certificates of commendation and appreciation are awarded directly from management.
Dissemination of safety information
We proactively disseminate important safety-related information that should be communicated to all JAL Group employees, such as messages from top management. This information is disseminated not only in paper form, but also via video. Videos containing safety-related content are uploaded to an internal portal site and can be viewed on demand at any time.